Total Cost of Ownership (TCO) is a financial estimate that considers the direct and indirect costs associated with acquiring, deploying, and maintaining a product or system over its entire lifecycle.
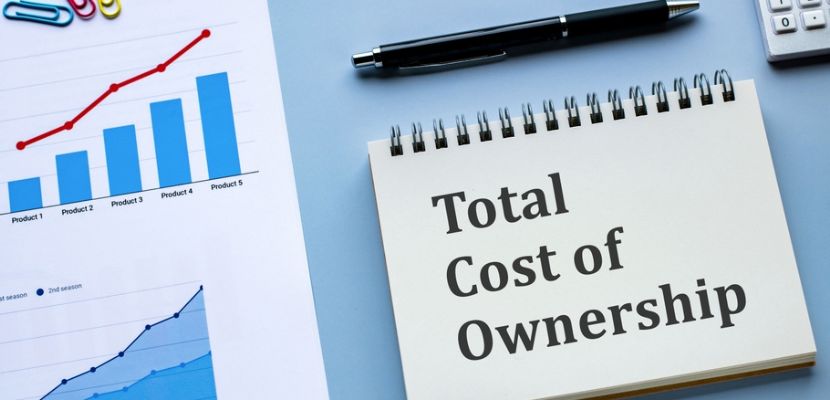
What Is Total Cost of Ownership (TCO)?
Total cost of ownership (TCO) is a comprehensive financial assessment that examines the overall expenses involved in acquiring, implementing, operating, and maintaining a product, service, or system throughout its lifespan. This analysis extends beyond the initial purchase price, incorporating both direct costs, such as purchase, installation, and operational expenses, and indirect costs, such as downtime, training, energy consumption, and support.
The purpose of TCO is to provide a more accurate understanding of the long-term financial impact by capturing all related expenses, which helps businesses make more strategic and cost-effective decisions. By considering factors like maintenance, depreciation, upgrades, and potential risks, TCO offers a full picture of what a particular investment truly entails over time, aiding in comparison between different options or approaches.
How to Calculate TCO?
Calculating TCO involves summing all the costs associated with acquiring, operating, maintaining, and eventually disposing of an asset or system over its entire lifecycle. Here’s how you can calculate TCO step-by-step:
- Determine the scope of the calculation. Clearly define the asset, system, or service whose TCO you are calculating. Establish its expected useful life or timeframe for analysis (e.g., 3 years, 5 years, etc.).
- Identify initial (capital) costs. Include the purchase price or upfront cost of acquiring the asset (e.g., hardware, software, machinery, or vehicles). Add costs for installation, initial configuration, deployment, or customization. Include any initial licensing fees for software or other intellectual property.
- Identify operating costs. Calculate energy use over the asset's lifespan. This is particularly important for equipment that consumes significant power, like data center servers or machinery. Account for materials needed to run the system, such as fuel, ink, or other resources. Include routine maintenance, support contracts, repairs, and upgrades over time. Factor in the cost of training employees or hiring specialists to operate or maintain the asset.
- Account for indirect costs. Estimate potential costs due to system downtime or productivity losses. This could include lost revenue, reduced efficiency, or penalties for delays. Add the costs associated with training personnel to use or maintain the asset. Include any additional costs to meet regulatory, security, or compliance requirements.
- Estimate end-of-life costs. Calculate costs for removing, disposing of, or recycling the asset once it reaches the end of its useful life. Subtract any potential resale value or trade-in value of the asset at the end of its life.
- Add up all costs. Once all the relevant costs have been identified and calculated, sum them to determine the total cost of ownership.
Factors that Influence TCO
Several factors influence the TCO across different industries and applications. Understanding these factors helps in making more accurate and informed investment decisions. Here are key factors that influence TCO:
- Initial purchase price. The upfront cost of acquiring an asset, such as hardware, software, machinery, or vehicles, is the most obvious component of TCO. However, it’s just one part of the total cost equation. Lower initial costs may seem attractive but could lead to higher long-term expenses.
- Installation and setup costs. After purchasing, many systems require additional investments to become operational, such as installation, configuration, integration with existing systems, or infrastructure upgrades. This can vary depending on the complexity of the product and the skills required.
- Operational costs. These are ongoing expenses needed to run the asset, including energy consumption, materials, consumables, and other resources necessary for day-to-day operation. For example, data centers and IT equipment have high energy costs, while machinery in manufacturing might require consumable parts.
- Maintenance and support. Regular maintenance, repairs, and support are crucial to keeping assets operational and efficient. This includes preventive maintenance, repairs due to wear and tear, technical support, and software updates or patches. Maintenance contracts or warranties can influence these costs.
- Downtime and reliability. The reliability of a system significantly impacts TCO. Frequent breakdowns or system downtimes result in lost productivity, operational inefficiencies, and potential revenue loss. The more reliable a system, the lower these indirect costs will be.
- Training and personnel costs. New assets often require personnel training for proper use or maintenance. This includes time and resources spent on employee training programs, certifications, or bringing in specialists. If the asset requires highly skilled personnel to manage it, ongoing labor costs can also be a major factor.
- Upgrades and scalability. Over time, systems may need upgrades or expansions to meet growing demands or to keep up with technological advancements. These upgrades can include software updates, additional hardware, or increased licensing fees. Scalability costs also affect the TCO, especially in IT environments where capacity can grow over time.
- Energy efficiency. Energy consumption plays a key role in TCO, especially for assets like servers, data centers, vehicles, or manufacturing equipment. Energy-efficient products often have higher upfront costs but lower long-term operational costs. Conversely, less efficient systems can drive up utility bills and cooling costs.
- Depreciation and resale value. Assets lose value over time, and this depreciation impacts their long-term cost. However, some assets retain more value than others and can be resold, offsetting the initial purchase price. Products with strong resale markets will have lower TCOs due to their higher residual value.
- Compliance and regulatory costs. Depending on the industry, assets may need to meet specific regulatory or compliance requirements, which could involve additional certifications, audits, or upgrades. Failing to comply with regulations could result in fines, which also adds to TCO.
- Decommissioning and disposal. At the end of an asset’s lifecycle, it may need to be safely decommissioned, recycled, or disposed of. Decommissioning costs include labor, legal fees, transportation, or environmental compliance requirements, especially in industries like IT or manufacturing where waste handling is regulated.
- Customization and integration. Customizing a system to meet specific business needs or integrating it with existing infrastructure can add significant costs. These modifications can be necessary for smooth operations but may result in more complex maintenance and higher support costs.
What Industries Use Total Cost of Ownership?
Total cost of ownership is widely used across various industries to assess the long-term costs associated with products, services, or systems. Some of the key industries that frequently utilize TCO include:
- Manufacturing. In manufacturing, TCO is applied to assess the costs of machinery, equipment, and production systems, including maintenance, downtime, and operational expenses. It helps manufacturers choose systems with the best value over their lifecycle.
- Information technology (IT). IT departments use TCO to evaluate hardware, software, cloud services, and network infrastructure. This includes the cost of acquisition, licensing, implementation, support, upgrades, and energy consumption, helping businesses select the most cost-effective technology solutions.
- Transportation and logistics. In transportation, TCO is used to determine the overall costs of vehicles, fleets, and logistics systems. This includes purchase prices, fuel consumption, maintenance, insurance, and depreciation, providing insights into which vehicles or systems offer the best long-term value.
- Construction. TCO is applied in construction to assess the lifecycle costs of buildings, equipment, and infrastructure. This includes the initial construction costs, maintenance, energy efficiency, and potential renovation or demolition costs, aiding in long-term project planning and budgeting.
- Energy and utilities. TCO helps energy and utility companies analyze the long-term costs of power plants, renewable energy systems, and other critical infrastructure. This includes upfront capital investment, operational costs, energy efficiency, and ongoing maintenance.
- Healthcare. In healthcare, TCO is used to evaluate the cost-effectiveness of medical equipment, devices, and IT systems. Hospitals and clinics assess both the upfront purchase costs and ongoing operational costs, such as maintenance, training, and compliance.
- Retail. Retailers use TCO to evaluate store infrastructure, point-of-sale systems, and logistics operations. This helps them optimize inventory management, customer service technologies, and store maintenance.
- Automotive. In the automotive industry, TCO is used to calculate the full cost of owning a vehicle, including purchase, fuel, maintenance, insurance, and depreciation. Consumers and fleet operators rely on TCO to determine the most cost-efficient vehicles.
Total Cost of Ownership Example
An example of total cost of ownership can be seen in the purchase of an enterprise IT server for a business. Here's how the TCO is evaluated in this scenario:
- Purchase price. The initial cost of the server might be $20,000. This is the upfront expense for acquiring the hardware.
- Installation costs. Additional costs of installing the server, including setting up the network, software, and storage, could add another $5,000.
- Operating costs. Over the server’s 5-year lifespan, the server will require ongoing electricity, cooling, and maintenance. Suppose electricity and cooling cost $2,000 per year and maintenance contracts cost $1,000 per year. Over 5 years, these operational expenses would total $15,000.
- Support and upgrades. Software upgrades and technical support might cost an additional $2,500 annually. Over 5 years, this amounts to $12,500.
- Downtime and productivity loss. If the server experiences downtime due to maintenance or technical issues, it could lead to lost productivity. For example, suppose downtime costs $3,000 over the server's lifespan due to interruptions in workflow.
- Decommissioning. At the end of its lifecycle, the server will need to be decommissioned and properly disposed of, which may incur costs of $1,500.
TCO Calculation
- Initial purchase price: $20,000
- Installation costs: $5,000
- Operating costs (electricity, cooling, maintenance): $15,000
- Support and upgrades: $12,500
- Downtime/productivity loss: $3,000
- Decommissioning: $1,500
Total Cost of Ownership (TCO) = $20,000 + $5,000 + $15,000 + $12,500 + $3,000 + $1,500 = $57,000